20
Feb
Equipment vibration isolation systems and techniques
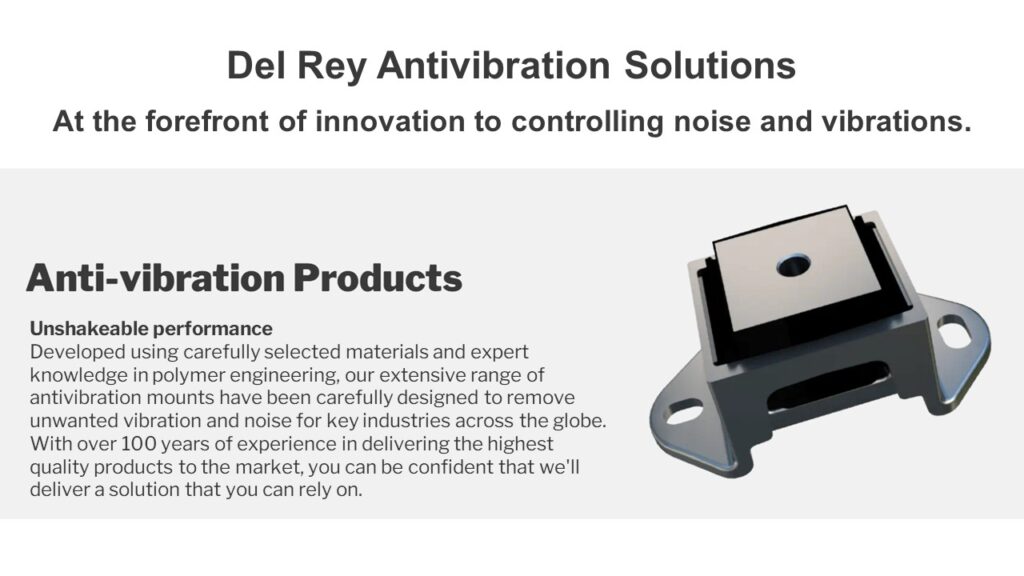
Table of Contents
- Equipment Vibration Isolation Systems and Techniques
- The Importance of Vibration Isolation
- Passive Vibration Isolation Systems
- Active Vibration Isolation Systems
- Applications of Vibration Isolation Systems
- Conclusion
Equipment Vibration Isolation Systems and Techniques
Vibration is a common problem in many industrial and mechanical systems. It can lead to reduced equipment performance, increased maintenance costs, and even safety hazards. To mitigate these issues, engineers have developed various vibration isolation systems and techniques. In this article, we will explore the different methods used to isolate equipment from vibrations and their applications in various industries.The Importance of Vibration Isolation
Vibrations can be caused by a variety of factors, including unbalanced rotating machinery, external forces, or even the natural frequencies of the equipment itself. These vibrations can have detrimental effects on the performance and lifespan of the equipment. For example, excessive vibrations can lead to premature wear and tear of components, misalignment, and increased noise levels. In some cases, vibrations can even cause catastrophic failures. By implementing effective vibration isolation systems, engineers can minimize the impact of vibrations on equipment. This not only improves the performance and reliability of the equipment but also enhances the safety of the surrounding environment and personnel.Passive Vibration Isolation Systems
Passive vibration isolation systems are widely used in various industries due to their simplicity and cost-effectiveness. These systems rely on the principle of decoupling the equipment from its surroundings to reduce vibrations. Some common passive vibration isolation techniques include:- Isolation Mounts: These mounts are designed to absorb and dampen vibrations by using materials with high damping properties, such as rubber or elastomers. Isolation mounts are commonly used in applications where the equipment is subjected to low-frequency vibrations.
- Spring Isolators: Spring isolators are used to isolate equipment from vibrations by utilizing the spring’s ability to absorb and dissipate energy. They are particularly effective in applications where the equipment is subjected to high-frequency vibrations.
- Viscous Dampers: Viscous dampers use the principle of fluid viscosity to dissipate vibrations. These dampers consist of a piston moving through a viscous fluid, converting the kinetic energy of vibrations into heat.
Active Vibration Isolation Systems
While passive vibration isolation systems are effective in many cases, they may not be suitable for applications with highly dynamic or unpredictable vibrations. In such scenarios, active vibration isolation systems are employed. Active systems use sensors and actuators to actively counteract vibrations in real-time. Some examples of active vibration isolation techniques include:- Active Damping: Active damping systems use sensors to measure vibrations and actuators to generate counteracting forces. These systems can adapt to changing vibration conditions and provide precise control over the equipment’s motion.
- Electromagnetic Suspension: Electromagnetic suspension systems use magnetic fields to levitate and isolate equipment from vibrations. These systems are commonly used in high-precision applications, such as semiconductor manufacturing or laboratory equipment.
- Piezoelectric Actuators: Piezoelectric actuators can rapidly change their shape in response to electrical signals. By integrating these actuators into the equipment’s mounting system, vibrations can be actively controlled and minimized.
Applications of Vibration Isolation Systems
Vibration isolation systems find applications in a wide range of industries and equipment. Some notable examples include:- Industrial machinery, such as pumps, compressors, and turbines, where vibrations can affect performance and reliability.
- Scientific and laboratory equipment, where precise measurements and experiments require minimal vibrations.
- Electronics manufacturing, where vibrations can lead to defects in delicate components.
- Medical equipment, such as MRI machines and surgical robots, where vibrations can impact accuracy and patient safety.
Conclusion
Vibration isolation systems and techniques play a crucial role in ensuring the performance, reliability, and safety of equipment in various industries. Passive systems, such as isolation mounts and spring isolators, provide cost-effective solutions for many applications. However, in cases where dynamic or unpredictable vibrations are present, active systems, such as active damping and electromagnetic suspension, offer precise control and mitigation. By implementing appropriate vibration isolation measures, engineers can minimize the detrimental effects of vibrations and enhance the overall efficiency and lifespan of equipment.
In-House remanufactured Carrier compressors
When it comes to air conditioning systems, Carrier is a name that stands out. Known for their high-quality products....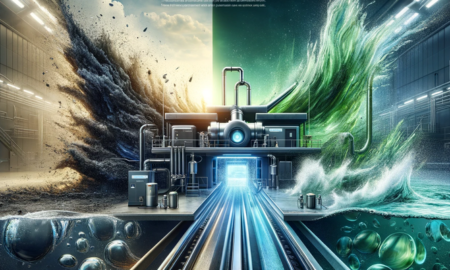
Revolutionizing Diesel Purification with Waagene Purifiner Technology
Diesel fuel quality is paramount for the efficient operation of engines...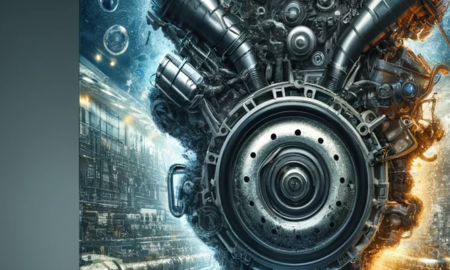